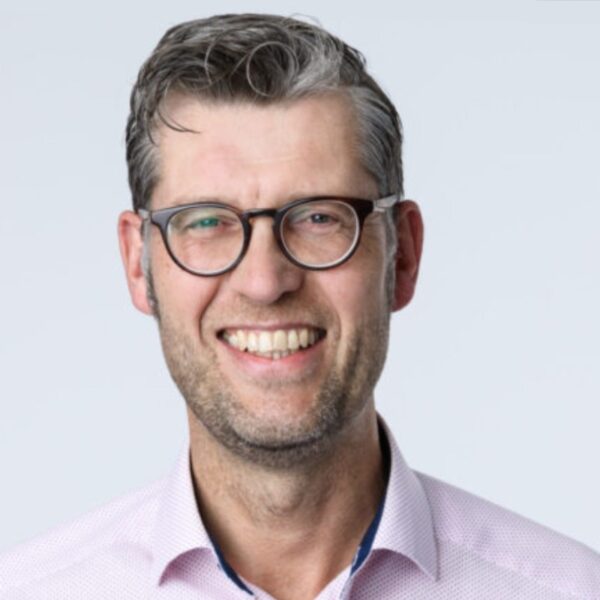
Outcome: accurate measurement of movements provide insights that can prevent life-threatening situations
Challenge: how to allow for heat expansion yet preventing displacements between boiler and pipes
When the boiler in the power station shows expansion when heated, the connected pipes must be able to maintain a completely tight connection during this expansion. This means that the pipes, which weigh thousands of kilos, must be extremely solid and strong and at the same time must be flexible enough to move with the expansion of the boiler. Simultaneously, the other side of the pipe will not move. The pipe is connected to rigid supports that must allow the horizontal expansion of the boiler, yet prevent horizontal displacement. These movements involve processes with small margins, in very dangerous conditions.
Solution: continuous sensor-based monitoring in environment where engineers cannot safely enter
The Sweco Monitoring Platform was put in place to measure the movements of the boiler and the connected pipe to an accuracy of 1/10 mm. Through continuous measurements with total stations all necessary information could be gathered in an environment where engineers cannot safely enter. Valuable information became available to the engineers of the plant. To make the 3D information understandable and to provide better insights in the movements, the deformations were shown in 3D models with the movements visualized as vectors.
Result: preventing damage and saving costs on the basis of 3D insights
The 3D insights revealed movements of the boiler that were not yet known. These unknown movements during expansion and under high temperatures have previously caused damage. Damage that could be traced back by means of the new data. Measures were taken to prevent the same kind of costly damage happening in the future. In addition to a safer plant, the monitoring of the boiler has also helped saved a lot of costs by providing insights into the deformations of crucial components and preventing future damage.